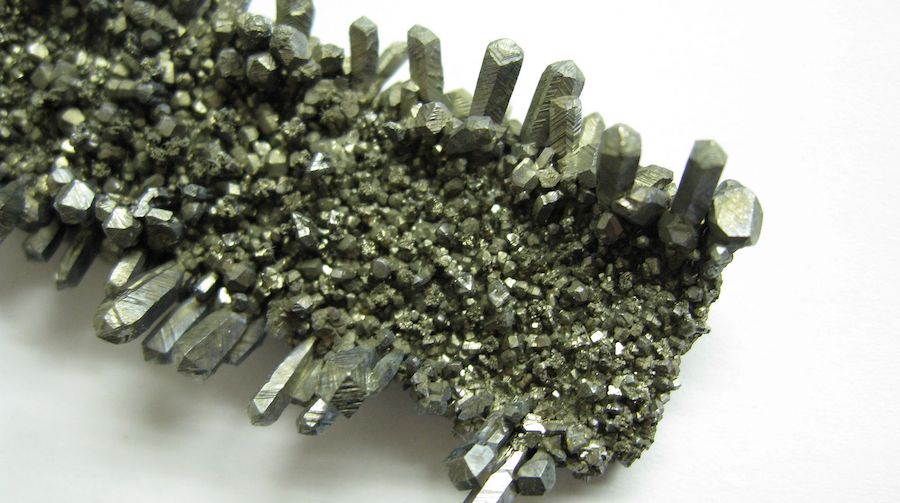
Plastic deformation describes the distortion that occurs at the atomic level when a sustained force is applied to a crystal. By using a new approach to systematically measure plastic deformation in crystals, the Japanese team led by Kyosuke Kishida has discovered that the process shows promise for use in high-temperature gas turbines.
Plastic deformation describes the distortion that occurs at the atomic level when a sustained force is applied to a crystal
In detail, the team measured plastic deformation in a niobium silicide called alpha-Nb5Si3. Tiny ‘micropillars’ of these crystals were exposed to very small amounts of stress using a machine with a flat-punch indenter at its end. The stress was applied to different faces of the sample to determine where and how plastic deformation occurs within the crystal. By using scanning electron microscopy on the samples before and after the test, they were able to detect the planes and directions in which deformation occurred.
This was followed by simulation studies based on theoretical calculations to further understand what was happening at the atomic level. Finally, the team compared the results with those of a boron-containing molybdenum silicide (Mo5SiB2) they had previously examined.
“We found that instantaneous failure occurs rather easily in alpha-Nb5Si3, which is in marked contrast to Mo5SiB2,” Kishida said in a media statement
This could mean alpha-Nb5Si3 is at a disadvantage compared to Mo5SiB2 for use as a strengthening component in metal-based alloys. Kishida and his team think, however, that this material’s inherent brittleness could be improved by adding other alloying elements.