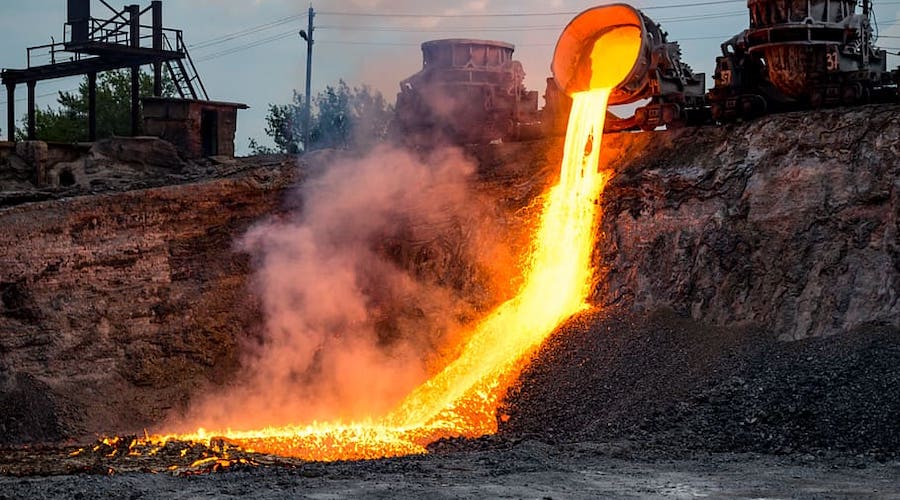
The development and testing of the new technique consisted of several stages. The first step was stabilizing the ladle slag in a solid state by adding borate glass —a cheap waste material that also requires recycling.
To obtain clinker from ladle slag, the team first calculated the conditions necessary for the production of clinker. These are the chemical composition of the processed mixture (charge) and the temperature range. Then, with the help of crushing and mixing, they obtained a charge with admixtures of silicon and aluminum-containing minerals alite, belite, celite, and brownmillerite.
Since out-of-furnace slag contains very little iron, it is usually not reused but sent to waste dumps
At the lab, the briquetted charge was heated in a furnace up to 1500-1600 degrees Celsius, until it completely melted, kept, and then slowly cooled. The experiments made it possible to find out that the clinker, in terms of the quality corresponding to industry standard, is formed from five slag compositions at a 10-minute exposure at a temperature of 1540-1560 degrees Celsius.
In the next stage, the group selected samples of waste from the electric furnace production that were similar in structure. These samples had a high iron content. After several melts —using coke as a carbonaceous reductant of iron simultaneously with Portland cement clinker— the scientists obtained cast iron that satisfies industry standards.
Subsequently, the technology of joint waste-free production of pig iron and Portland cement clinker was successfully tested at the Klyuchevskoy Ferroalloy Plant.
In the course of test heats, the developers came to the conclusion that in order to avoid overheating and control temperatures and save money, a cheaper rotary tilt furnace should be used, not an arc furnace.
Clinker was formed from the charge, which was fed into the rotary tilting furnace, as a result of mixing, reduction, and melting cast iron and slag residue. Subsequent mixing of clinker with gypsum dihydrate and firing the mixture in a kiln resulted in the formation of Portland cement, the most widely used type of cement.