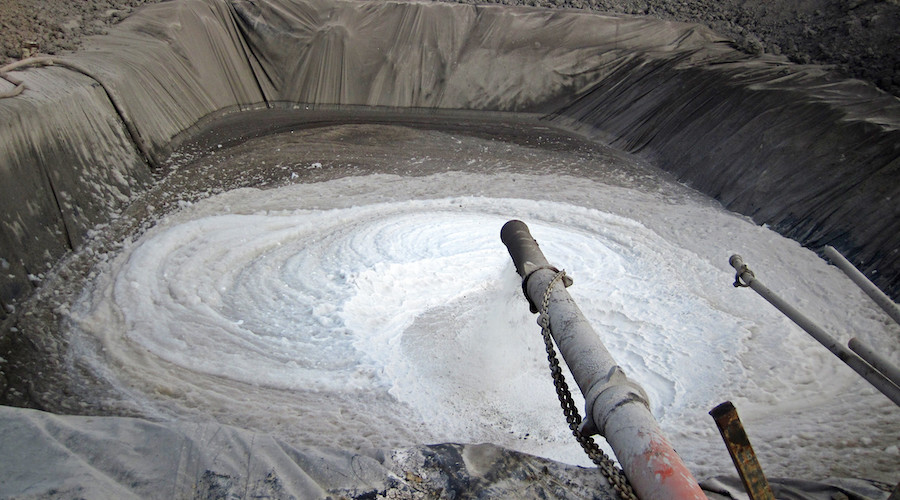
After describing that, at present, lithium is most commonly sourced from salt brines in South America using solar evaporation, a costly process that can take years and wastes much of the lithium along the way, the team behind the new study explains that they designed specific membranes to efficiently recover the metal from water generated in oil and gas production.
Crown ethers had not previously been applied or studied as integral parts of water treatment membranes, but they can target specific molecules in water — a key process for lithium extraction
At the heart of the discovery is a novel polymer membrane they created using crown ethers, which are ligands with specific chemical functionality to bind certain ions. Crown ethers had not previously been applied or studied as integral parts of water treatment membranes, but they can target specific molecules in water — a key process for lithium extraction.
In most polymers, sodium travels through membranes faster than lithium. However, in these new materials, lithium travels faster than sodium, which is a common contaminant in lithium-containing brines. Through computer modelling, the team discovered why this was happening. Sodium ions bind with the crown ethers, slowing them down, while lithium ions remain unbound, enabling them to move more quickly through the polymer.
The findings represent a new frontier in membrane science that required above-and-beyond collaboration between The University of Texas at Austin and the University of California, Santa Barbara in such areas as polymer synthesis, membrane characterization and modelling simulation.
According to the researchers, the proposal is exciting because the calculations show that just a single week’s worth of water from hydraulic fracturing in Texas’ Eagle Ford Shale has the potential to produce enough lithium for 300 electric vehicle batteries, or 1.7 million smartphones.
In their view, this example shows the scale of opportunities for this new technique to increase lithium supply and lower costs for devices that rely on it.