Li-ion battery recycling may not take off before 2030 – report
According to Max Reid, lead author of the report, underneath the surface of this electric future lies a relatively young supply chain struggling to keep up.
“The Li-ion battery demand market can fluctuate over months and expanding upstream and midstream to produce battery materials involves lead times of several years,” he said. “As it is a new industry, there is limited historic capacity to flip the switch on, and yet many see this as a ripe environment for recycling to make a tangible impact.”
However, Reid pointed out that battery recycling focuses – at least at present- on the portable electronics market because recyclers benefit from technologies with an easily accessible battery, compared with EV batteries.
“EV-packs are complex to disassemble into individual cells, so recyclers are left to discharge packs in conductive baths before mechanically shredding them into a mix of constituent materials,” he wrote in the dossier. “Furthermore, currently new batteries cost less to produce, hence disincentivizing battery recycling as the value of recovered material is reduced.”
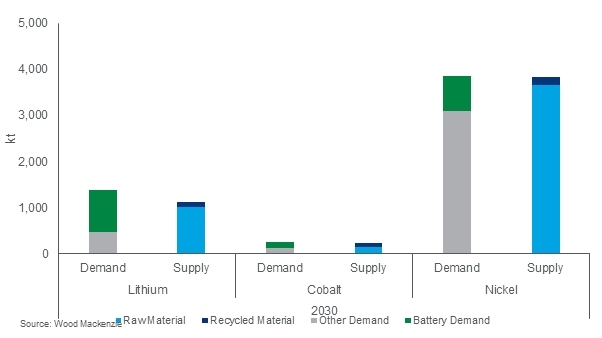
In addition to the prior, battery manufacturers are leaning towards using cheaper materials, a situation that, according to WoodMac, pushes recyclers to increase the efficiency of their processes to maintain profit. Moreover, the introduction of new materials such as solid-state electrolytes will likely require recyclers to retrofit their processes.
“This decade will see the supply chain further establish itself to be able to supply vast quantities of battery-grade chemicals and cathodes to cell manufacturers, whilst recyclers will struggle with the large mass and complexity of EV-packs,” Reid said.
As an example, the expert mentioned that a new cathode facility will produce 50 kilo-tonnes per annum (ktpa) of NMC or nickel, manganese and cobalt material, whilst a recycling facility will typically process 5-10 ktpa of e-waste – the former equating to roughly 400,000 battery EVs annually and the latter taking in just roughly 30,000 EV-packs yearly.
Reid also said that the lack of recyclable feedstock is a major barrier.
In his view, even though EV manufacturing is set to boom before 2030, the number of end-of-life batteries available for recycling will remain limited for two main reasons: EV penetration at the beginning of the decade is much lower than at the end, and EVs having an increasingly long lifespan reaching up to 15 years.
“The lack of available secondary supply from recycling is evident, and yet the recycling sector is already scaling up quite aggressively,” the document reads.
Wood Mackenzie’s data show that the total capacity of planned recycling facilities will still overshoot feedstock in 2030 when EoL EV numbers begin to ramp up. The resulting supply imbalance is, thus, expected to leave independent recyclers, especially in North America and Europe, in a scramble for used EV batteries.
“China, which has a mature and large reuse and refurbishment sector for portable electronics, benefits from proximity to the midstream,” the dossier states. “Chinese recyclers benefit from greater integration with nearby cathode production plants, so Chinese recyclers can regularly bid much higher prices for used batteries than their Western counterparts. Until North America and Europe have developed more integrated raw material supply chains, China will remain the most appealing location for battery recycling.”
For Reid, limitations on feedstocks mean that only the large and integrated recyclers will likely survive and reap the rewards in later years. This means that new entrants into the space should be cautious when looking at bullish expectations for Li-ion recycling.