While industrial extraction from these wastes commonly involves leaching with strong acid, a time-consuming, non-green process, the Rice lab heats fly ash and other materials (combined with carbon black to enhance conductivity) to about 3,000 degrees Celsius in a second. The process turns the waste into highly soluble “activated REE species.”
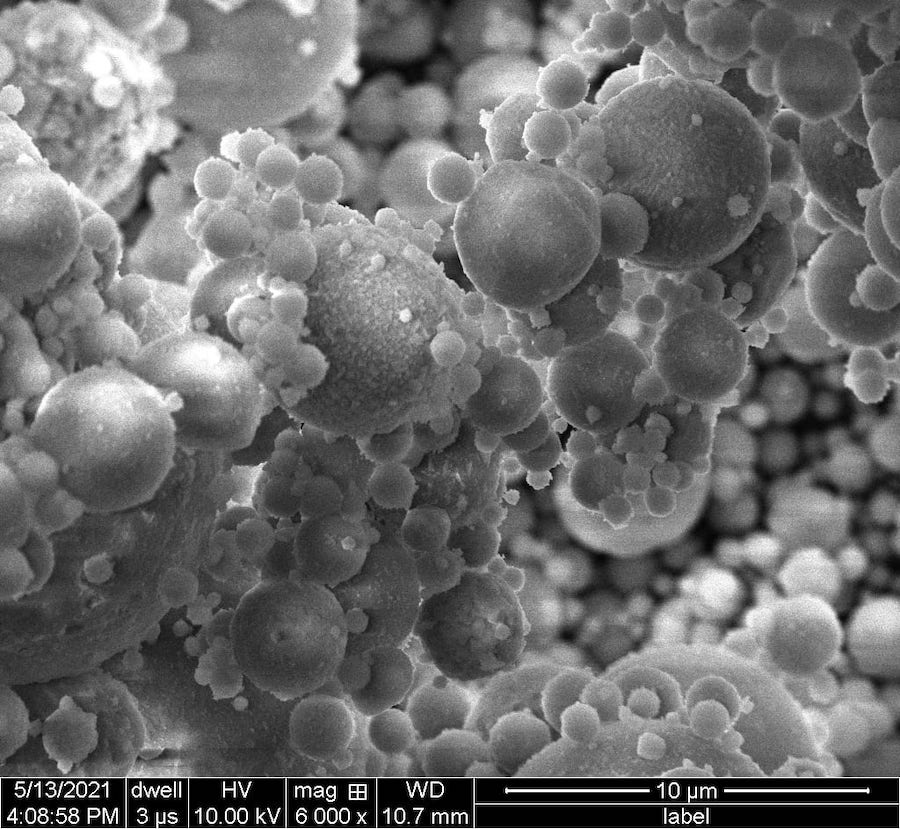
According to James Tour, senior author of the study, treating fly ash by flash Joule heating breaks the glass that encases these elements and converts REE phosphates to metal oxides that dissolve much more easily.
The new process also yields more product by using a much milder 0.1-molar concentration of hydrochloric acid instead than the 15-molar concentration of nitric acid used in existing industrial processes to extract the materials.
In experiments led by postdoctoral researcher and lead author of the paper Bing Deng, the researchers found flash Joule heating coal fly ash (CFA) more than doubled the yield of most of the rare earth elements using very mild acid compared to leaching untreated CFA in strong acids.
“The strategy is general for various wastes,” Bing said. “We proved that the REE recovery yields were improved from coal fly ash, bauxite residue and electronic wastes by the same activation process.”
For Bing, the generality of the process makes it especially promising, as millions of tons of bauxite residue and electronic waste are produced every year.
“The US used to mine rare earth elements, but you get a lot of radioactive elements as well,” Tour said. “You’re not allowed to reinject the water, and it has to be disposed of, which is expensive and problematic. On the day the US did away with all rare earth mining, the foreign sources raised their price tenfold. Our process tells the country that we’re no longer dependent on environmentally detrimental mining or foreign sources for rare earth elements.”