The rare earth problem must be solved by innovating, not just playing catch up
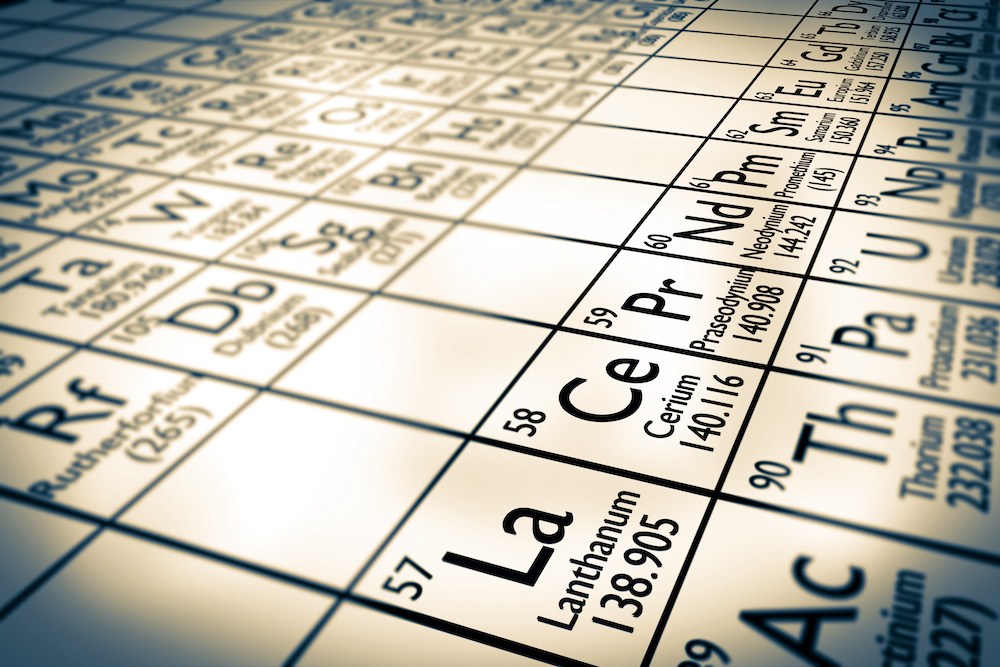
The solution that dominates today’s narrative, both in the US and Europe, is an increase in domestic supply. Digging new mines. Building processing and manufacturing capabilities for finished products from the ground up. But, as critics in the Wall Street Journal have pointed out, these solutions will likely fall short. Mining permits are often slow and hard to come by. Rare earth mining poses massive environmental issues.
The necessity of subsidized solutions raises financial sustainability concerns. Replicating the competitiveness of Chinese rare earth production is a losing game of catch up – China benefits from massive scale and forty years of relatively uncontested expertise development.
The answer is not to bet it all on ramping up domestic rare earth supply, it’s to take a lesson from the companies who, a decade ago, faced the 2011 Rare Earth Crisis and came out stronger – win through innovation. We have three routes to do so: design optimization, alternative materials, and recycling.
Design optimization to reduce rare earth content is the innovation we saw most commonly in 2011 – automakers found ways to switch from rare earth neodymium magnets to weaker ceramic magnets, oil companies used less lanthanum in refining, electronics manufacturers redesigned to reduce the need for dysprosium. We’re seeing it again today – both in established companies, like HVAC giant Daiken committing to phase out all rare earths by 2025, and startups, like the collaboration between California-based Wind Harvest and UK firm GreenSpur that bucks traditional design conventions to deliver a rare earth-free wind turbine.
Design optimization can be encouraged by fostering partnerships between incumbents and innovative new firms, as well as targeted procurement efforts to incentivize design away from rare earths. It is a critical lever to reduce dependence and our most promising source of quick wins. However, we use rare earths for a reason, so using fewer is not a solution on its own.
Alternative materials didn’t factor into the 2011 solutions with MIT providing a simple explanation at the time: “Inventing substitutes and getting them into motors will take years”. Fortunately, the last 10 years didn’t go to waste.
In September 2011, ARPA-E (the Department of Energy equivalent to DARPA, which famously invented the internet) launched their Rare Earth Alternatives in Critical Materials (REACT) program, funding 14 projects at universities, government labs, and private companies to reduce US rare earth dependency.
Today, the REACT investment is bearing fruit with iron nitride and cerium-based compounds. Researchers in Germany have done the same with iron phosphide. Though some of these alternatives are still academic, others are on the horizon of commercialization. Toyota is already making use of a technique to partially substitute scarce rare earth elements with abundant ones in next-generation Prius motors.
While material science holds great uncertainty, a decade of work developing and refining solutions means that this time it’s different. Properly supported for scale-up, alternative materials are potentially game changing.
And lastly there is recycling. While demand growth means we cannot solely recycle our way out of supply challenges, there will always be uses where rare earths cannot be designed out and alternative material properties are incompatible – here recycling will be critical to augment any realized domestic supply. This is taking place at a small scale today – like Texas-based Urban Mining Company and Geomega Resources in Canada – but recent estimates still suggest only 1% of rare earths are recycled. Experts are pushing for government intervention to mandate recycling, increase recovery rates, and reduce costs.
Increasing domestic rare earth supply is a worthwhile effort, but it is foolish as a standalone approach. If the US, Europe, and their allies hope to mitigate the impact of China’s rare earth dominance, they must diversify their bets and change the dominant narrative. Not playing catch up, but supporting innovation in design optimization, alternative materials, and recycling to jump ahead.
Tom Grainger is the Director of Strategy & Business Development at Niron Magnetics. He advises on climate and innovation policy for various nonprofit organizations.