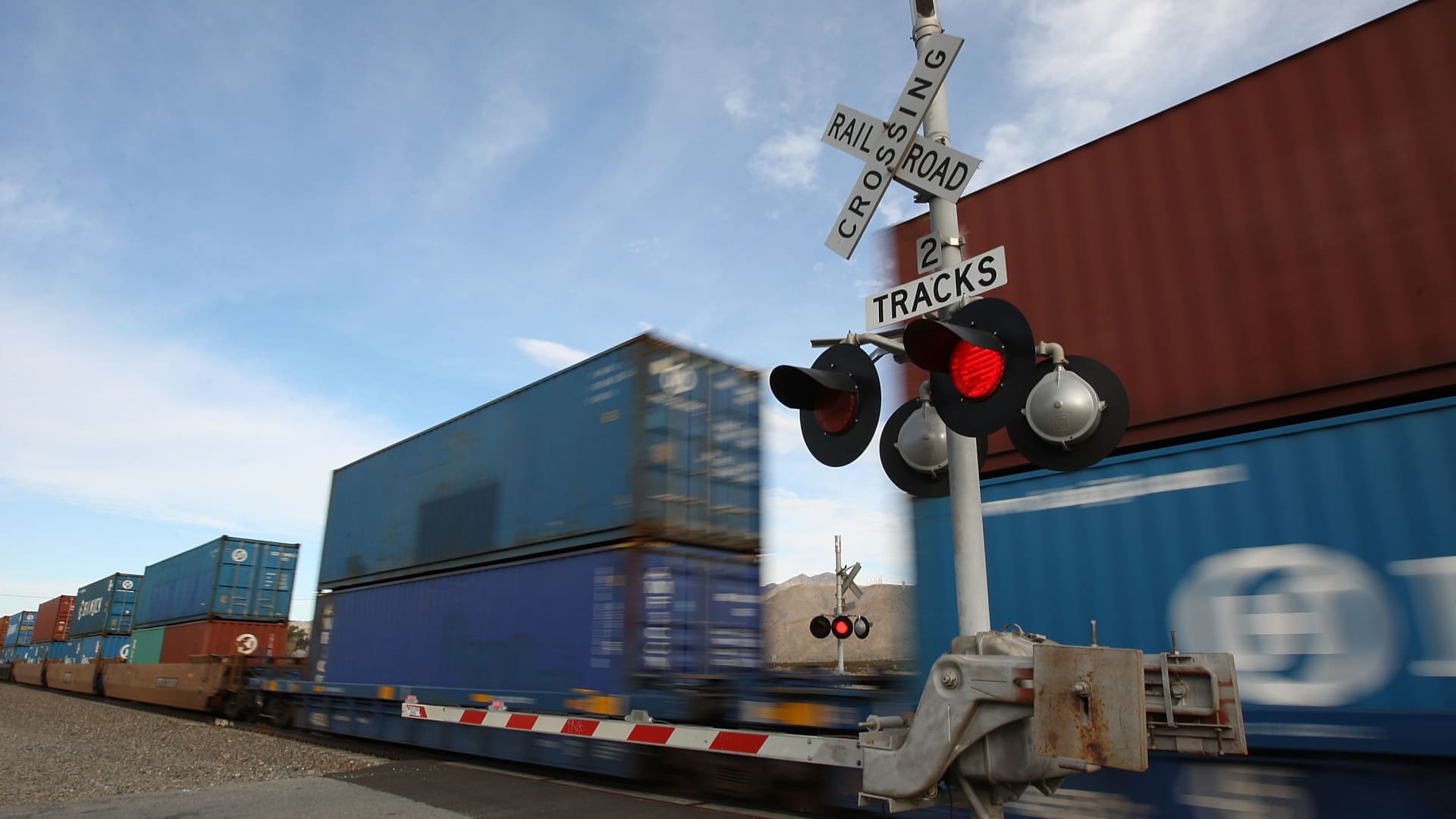
Rail congestion from Berkshire Hathaway subsidiary BNSF and Union Pacific, the railroads servicing the West Coast ports, is getting worse and slowing down container processing at the nation’s largest port complex.
Slowdowns involving containers limits future availability and constricts supply, which can spark an increase in container prices. Congestion was one of the reasons behind the surging freight prices during the pandemic, prices that have been passed onto the consumer contributing to inflation.
“60% of our long dwelling containers are scheduled to go on the rail,” said Gene Seroka, executive director of the Port of Los Angeles. “Our land capacity is at 90% .”
The increase in time of the import containers staying in the port is one of the key metrics being tracked by the CNBC Supply Chain Heat Map.
A terminal’s land capacity for the efficient movement of containers is 70-75% so the trucks and equipment can easily move.
Vessel anchorage to berth times are steadily improving, allowing for more boxes to land onto terminals, but the fact that rail car capacities are limited will mean future containers may start stacking up in rail yards waiting to be loaded and moved appropriately, according to Captain Adil Ashiq, United States Western Region executive for MarineTraffic. “As these containers stack up, terminals may eventually run out of space, and be unable to take new imports – a slippery slope which may cause vessel dwell times to once again increase, or cause the carriers to instead call another port altogether and avoid the slowdown,” Ashiq said.
Los Angeles, Long Beach wait times tick up
The wait time for containers leaving the ports of Los Angeles and Long Beach continues to tick up. The dwell time for a container bound for rail is 7.5 days at the Port of Los Angeles, and a little over 8 days at the Port of Long Beach.
“We are at a point of inflection as to the rail bottlenecks, including the lack of rail cars at the nation’s largest and most significant container gateway,” said Mario Cordero, the executive director for the Port of Long Beach.
The Port of Oakland’s two rail yards are near-dock, not “on-dock” like the ports of Los Angeles and Long Beach. Port officials told CNBC roughly 10% of its imports are moved by train. The Pacific Northwest, however, relies on rail to move its imports and exports. The Northwest Seaport Alliance (NWSA) is comprised of the ports of Tacoma and Seattle. These ports, like the ports of Los Angeles, Long Beach, and Oakland are landlord ports. But unlike the ports of Los Angeles and Long Beach, which track the dwell times of their containers bound for rail, the NWSA does not and referred CNBC to the terminals who do not share that information with the NWSA. The terminals did not respond to requests for comment.
According to the CNBC Supply Chain Heat Map, the dwell times of an import container leaving the port of Tacoma or Seattle either by truck or rail is over 16 days for Seattle, and 8 days for Tacoma.
“The decision of where a container bound for rail goes is decided by the ocean carriers,” said Jack Hedge, executive director of the Utah Inland Port Authority. “The carriers are limiting which inland ports to go to. If they were flexible to diversify their rail routes, it would ease the bottlenecks on the rails and free up congestion. But that would mean their containers would be inland longer.”
Union Pacific said they were unable to comment on the congestion because they were in a quiet period due to upcoming earnings.
BNSF’s plan to regain momentum
BNSF, responding by email, said operational safety, service and efficiency are aligned throughout its network and “while this momentum is inconsistent at times, we are on the right path toward delivering better service performance.”
BNSF noted that it deployed additional locomotives to its active fleet in April and May. “We are continuing to evaluate and adjust the number of additional units that may join the fleet in alignment with freight volumes,” it stated.
BNSF is also focused on turning inventory in Chicago to get cars back to Southern California as quickly as possible. “As we move through June, our efforts are beginning to yield positive results with greater velocity and productivity levels,” its email stated.
BNSF plans to hire approximately 3,000 additional employees this year, which includes new personnel for its engineering, mechanical, and dispatcher teams, and nearly 1,800 train, yard, and engine (TY&E) members. More than 257 (TY&E) members have completed their training and 237 more are anticipated to complete their training in the next 90 days.
East Coast ports are taking more share
The congestion at the ports and the threat of labor slowdowns or strikes by longshoremen have led to a parade of trade moving away from the West Coast to the East Coast.
“From January through the month of May, we had an 11.5% increase in import containers,” said Bethann Rooney, director for the Port of New York and New Jersey. “6.5% of that volume was cargo shifted from the west coast ports.”
Rooney said the ports have also seen an unusually early arrival in holiday items, including Christmas trees into the port, as well as winter apparel. Household appliances are also part of the long dwelling containers.
The market share of trade captured by the east coast can be tracked by the volume of containers.
The Port of Savannah, which is seeing vessels at anchorage for 10 days describes, said the volumes it is processing are “staggering.”
“We expect 155 vessel calls in the month of July. 39 of these vessels, or 25%, are unplanned,” said Edward Fulford, spokesman for the Georgia Ports Authority. “This is the highest volume of ad hoc and new service vessels the Port of Savannah has experienced to date. We know that the labor talks and delayed access to rail are prompting a significant shift in vessel calls to the East Coast.”
The Port of Norfolk is seeing a trend of U.S. importers circumventing the West Coast congestion and using the port’s rail services.
“Until [this] April, moving cargo east-to-west from Virginia to California by rail was unheard of,” said Tom Capozzi, chief sales and marketing officer of Virginia International Terminals.
He said several cargo owners, importers in California who needed reliability and predictability restored in their supply chains, started using its on-dock rail service. He added, “We are seeing some cargo owners in California show interest in using the Hapag-Lloyd’s reworked MGX service where the containers that arrive on Hapag Lloyd ocean carriers are then moved by rail to Chicago and then loaded onto a UP rail car bound for the West Coast.”
The first Hapag-Lloyd MGX service had nearly 1,000 containers that were loaded onto rail bound for California.
The railroads that service the East Coast ports are Norfolk Southern and CSX.
Railroad union dispute
The Class I freight railroads and the twelve rail unions have been embroiled in a labor dispute since 2020 and are currently in a 30-day “cooling off period”. The U.S. Chamber of Commerce recently sent a letter to President Biden, copying Labor Secretary Marty Walsh and Transportation Secretary Pete Buttigieg, urging the president to get involved.
“A strike by the railroad workers would be more disruptive than a longshoreman strike on the West Coast,” Hedge said. “This would impact all trade.”
The National Mediation Board (NMB), an independent U.S. federal government agency that facilitates labor-management relations within the nation’s railroad and airline industries, is scheduling a public interest meeting, set to begin on July 12.
The labor strife in Europe is an example of how labor at the rail or ports stops or slows down trade. Labor negotiations are at an impasse in the German ports and the congestion contagion has spread to other European ports.
In an advisory to clients, METRANS Group explained they would enact a 48-hour suspension of trains as a result of 200 of its railcars waiting in front of the CTA terminal in Hamburg.
Crane Worldwide Logistics says the current congestion building at the European ports will take over eight weeks to clear and will only increase as the logjam builds up. These containers waiting for export include autos, auto parts, and IKEA furniture and household items.