South Star Battery Metal secures construction permit for graphite mine in Brazil
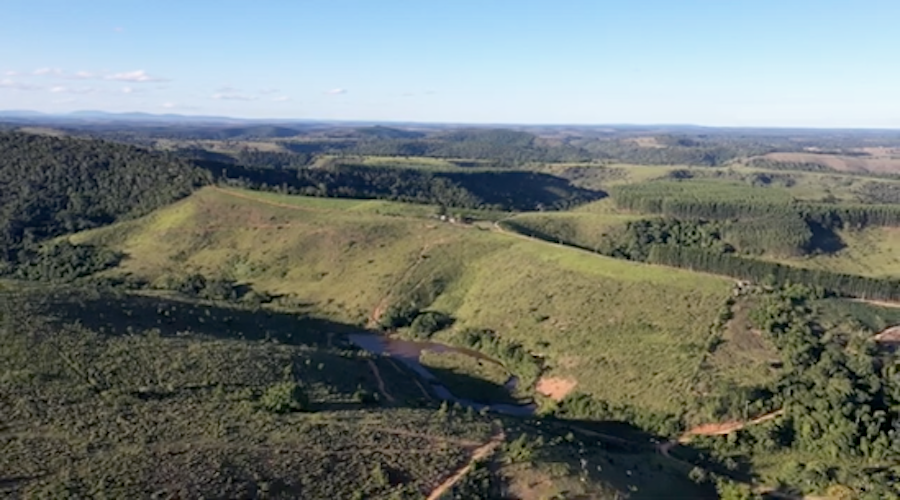
“We presented additional details about Santa Cruz and our planned growth through Phase 2 (25,000 tonnes per year of concentrates) and Phase 3 (50,000 tpy of concentrates),” chief executive Richard Pearce said of the meetings.
South Star, which aims to start production at Santa Cruz by the end of 2023, said the mine will be the first major industrial facility in the municipality and one of the largest in the region as it scales operations.
It added that its Santa Cruz graphite project was the first of a series of industrial and battery metals projects that plans to bring into production.
The Vancouver-based company also noted that its next project in the pipeline is a development project in Alabama, United States, located in the middle of a developing electric vehicle, aerospace and defence hub.
Underestimated
Demand for graphite, an overlooked mineral that is a key ingredient for the electrification of vehicles, is expected to soar.
The lithium-ion battery used to power electric vehicles is made of two electrodes — an anode (negative) on one side and a cathode (positive) on the other. The resistant material, an excellent conductor of electricity and heat, is the only one that can be used in the anode, there are no substitutes.
It is also the largest component in lithium-ion batteries by weight, with each battery containing 20-30% graphite. But due to losses in the manufacturing process, it takes 30 times more graphite than lithium to make the batteries.
According to the World Bank, graphite accounts for nearly 53.8% of the mineral demand in batteries, the most of any. Lithium, despite being a staple across all batteries, accounts for only 4% of demand.
Consultancy Benchmark Mineral Intelligence (BMI) sees a roughly 20,000 tonne graphite deficit by the end of 2022, versus a similar-sized surplus in 2020.