Metallic materials’ fatigue strength can now be quickly determined
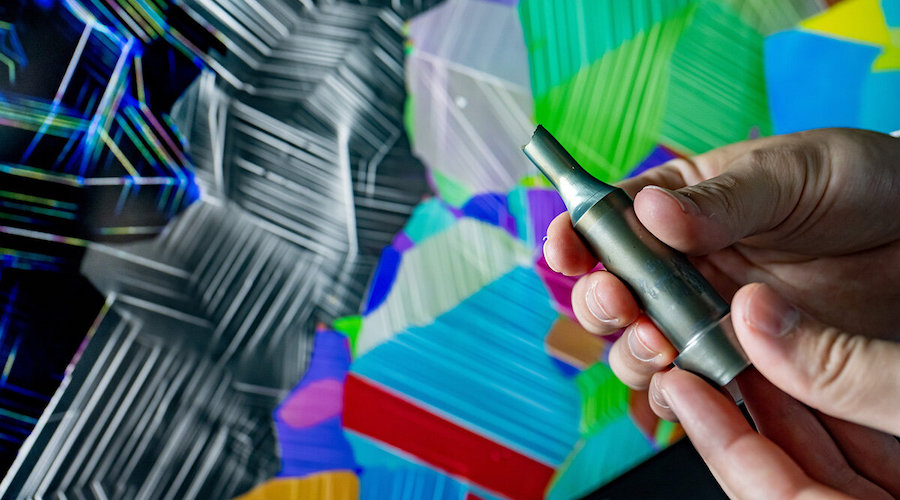
In a new study published in the journal Science, the researchers report that automated high-resolution electron imaging can capture the nanoscale deformation events that lead to metal failure and breakage at the origin of metal failure.
The new method helps scientists to rapidly predict the fatigue strength of any alloy, and design new materials for engineering systems subject to repeated loading.
According to the Illinois group, fatigue of metals and alloys—such as the repeated bending of a metal paperclip that leads to its fracture—is the root cause of failure in many engineering systems. Defining the relationship between fatigue strength and the microstructure is challenging because metallic materials display complex structures with features ranging from the nanometer to the centimetre scale.
“This multiscale issue is a long-standing problem because we’re trying to observe sparse, nanometer-sized events that control macroscopic properties and can be captured only by investigating large areas with fine resolution,” co-lead researcher Marie Charpagne said in a media statement.
“The current method for determining fatigue strength in metals uses traditional mechanical testing that is costly, time-consuming and does not provide a clear picture of the root cause of failure.”
In the current paper, Charpagne and her colleagues found that the statistical investigation of the nanoscale events that appear at the metal surface when deformed can inform the fatigue strength of metals.
The team is the first to uncover this relationship using automated high-resolution digital image correlation collected in the scanning electron microscope—a technique that compiles and compares a series of images recorded during deformation. This relation was demonstrated on alloys of aluminum, cobalt, copper, iron, nickel, steel and refractory alloys used in a large variety of key engineering applications.
“What is remarkable is that the nanoscale deformation events that appear after a single deformation cycle correlate with the fatigue strength that informs the life of a metallic part under a large number of cycles,” co-lead researcher Jean-Charles Stinville said. “Discovering this correlation is like having access to a unique deformation fingerprint that can help us rapidly predict the fatigue life of metallic parts.”
For Stinville and Charpagne, designing metallic materials with higher fatigue strength and longer life means safer, more resilient and durable objects, which is why they believe their work has societal, environmental and economic impacts.
“I think this work will define a new paradigm in alloy design,” Charpagne said.